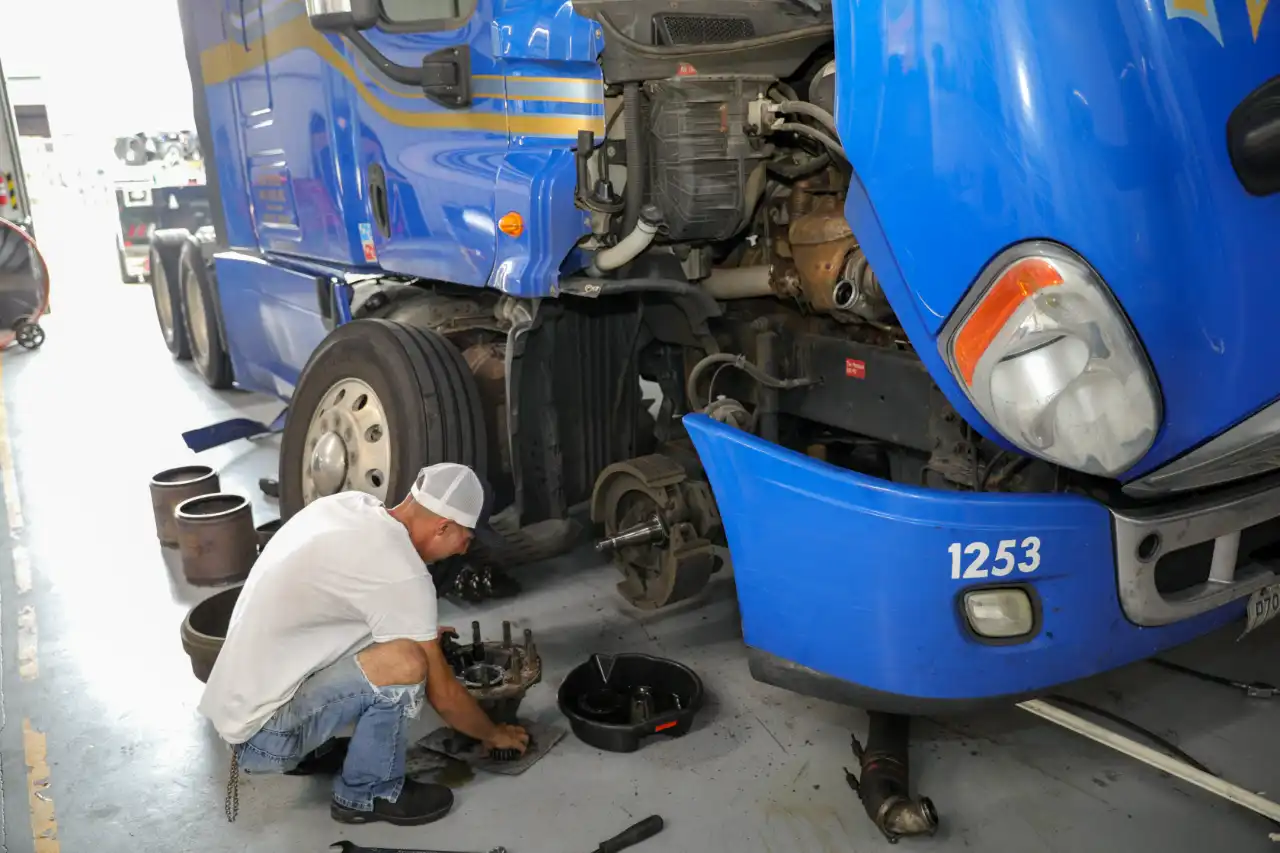
When it comes to food and grocery deliveries, efficient fleet management is the heartbeat of your operation. Every minute counts, every route matters, and every breakdown could mean spoiled goods or empty shelves. In the Texas heat, where delivery timelines are tight and customer expectations are tighter, poor fleet coordination can be catastrophic.
Whether you're delivering fresh avocados or frozen meat, the logistics behind getting groceries from warehouse to doorstep rely on precision, reliability, and strategy. That’s where fleet efficiency comes into play.
Cold Chain Logistics and Time Sensitivity
Groceries aren’t your typical cargo. You’re dealing with temperature-sensitive products, expiration dates, and time-critical deliveries. A late or mismanaged shipment can lead to spoiled goods and financial loss. Efficient fleet management ensures:
- Optimal route planning to reduce travel time and maintain cold chain integrity.
- Proper reefer unit maintenance to keep produce at the required temperatures.
- Driver coordination to minimize delays or last-minute cancellations.
A single missed delivery can break contracts and shatter customer trust—two things you can’t afford in the food industry.
Fuel Efficiency and Cost Control
Texas fleets cover long distances. That means fuel efficiency is key to cost control. Through smart routing, idle-time tracking, and consistent preventive maintenance, your trucks consume less fuel and face fewer mechanical issues.
Small actions, such as reducing excess idling or maintaining proper tire pressure, can save thousands in annual fuel costs. And with the price of diesel these days, if you add up those savings across your entire fleet, you've got a serious financial edge.
Downtime is the Silent Profit Killer
Let’s be honest: nothing disrupts a delivery schedule like a truck that won’t start. Without proper fleet oversight, trucks may miss critical maintenance intervals, leading to sudden breakdowns. That’s bad news when you’re hauling perishable goods in a time-sensitive delivery window.
Proactive management tools can alert you to:
- Transmission fluid issues before the gears start slipping.
- Cooling system problems that could lead to overheating.
- Worn brake shoes could delay stopping distances in heavy traffic.
Staying ahead of these issues means you’re not calling for roadside help during rush hour with a truck full of dairy.
Compliance, Safety, and Driver Morale
Grocery haulers must adhere to strict regulations, including weight limits and emissions standards. Well-managed fleets track compliance and reduce the risk of fines or failed inspections. Drivers also benefit from well-maintained trucks, leading to higher morale and lower turnover.
In a state like Texas, where long-haul routes and tight delivery windows are the norm, happy drivers are productive drivers. Efficient fleet systems enable drivers to focus on the road, not their next breakdown.
Data-Driven Decisions: Tech Meets Trucking
Modern fleet management systems offer real-time analytics to inform informed decision-making. Want to know which driver has the best delivery times? Which truck uses the most DEF? Which route burns the most fuel?
These systems help you:
- Improve delivery times.
- Balance load assignments.
- Reduce mechanical wear.
Smart fleets aren’t just reactive—they’re strategically proactive, planning for the next week, month, and season before issues arise.
Scalability Without Chaos
As your delivery operation grows, so does your risk—unless your systems grow with you. Proper fleet management ensures:
- Smooth vehicle acquisition and decommissioning.
- Simplified scheduling for drivers.
- Consistent service records across vehicles.
This allows you to scale without losing track of assets or falling behind on DOT inspections.
Weathering Texas-Sized Challenges
Between scorching summers and unexpected freezes, Texas throws plenty at your trucks. Efficient fleet oversight means preparing for every curveball:
- Swapping to season-specific coolant mixtures.
- Monitoring air dryer systems to avoid frozen brake lines in winter.
- Ensuring alternators and batteries are up for extreme heat loads.
Preparation through data and maintenance is the difference between making it to the store on time or making a costly detour.
The Bottom Line
Fleet management isn’t just about logistics—it’s about ensuring the lettuce is crisp, the milk stays cold, and customers never question your reliability. From routing to compliance to preventive maintenance, your fleet is the engine driving your success in the grocery game.
Don't let inefficiency eat into your margins—start optimizing your fleet today with the help of our experts at Integrity Fleet Services!
More Articles
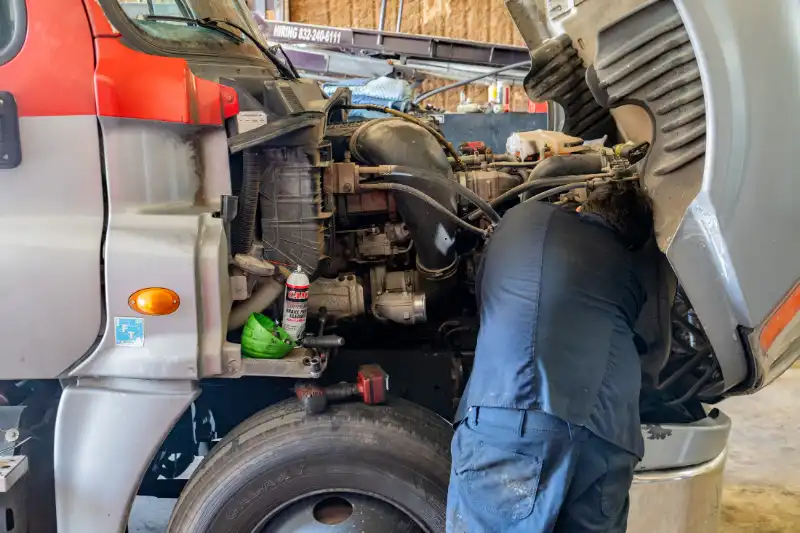
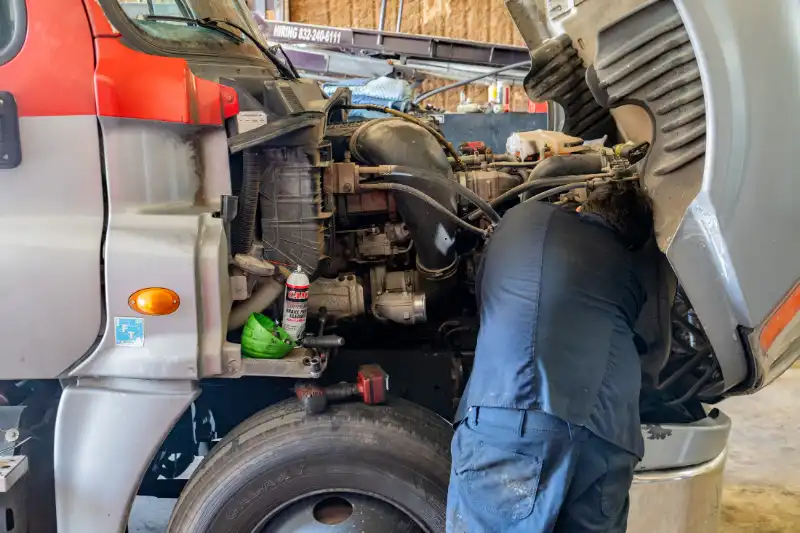
How to Train Drivers for Your Food and Grocery Fleet
How to Train Drivers for Your Food and Grocery Fleet
Food delivery fleets succeed or fail by their drivers. From reefer tech to FSMA compliance, this guide covers everything you need to train drivers for perishable freight—from safety and sanitation to customer service and Texas-specific road challenges. Ask ChatGPT
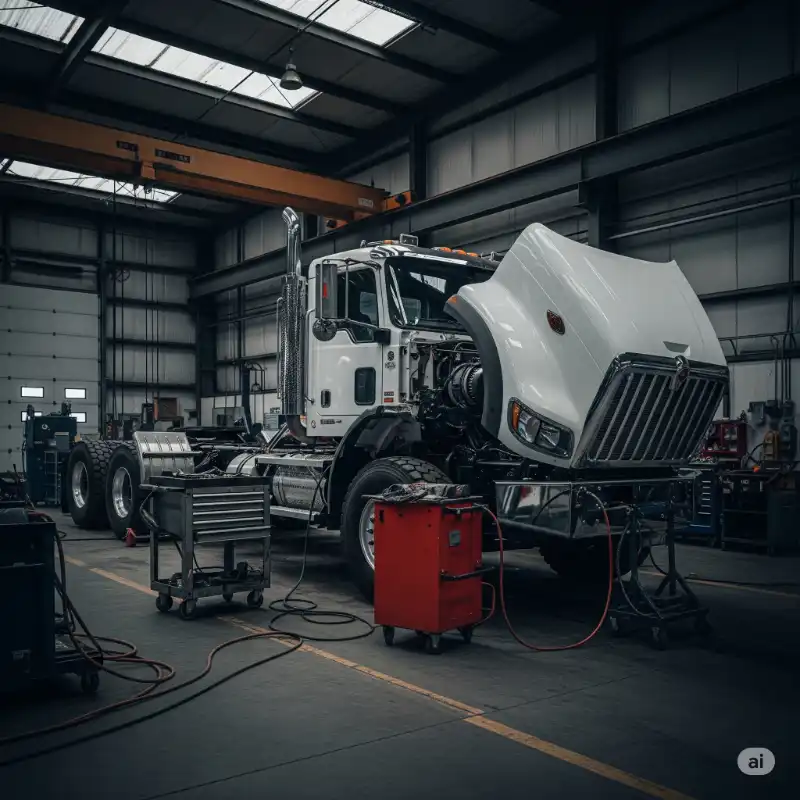
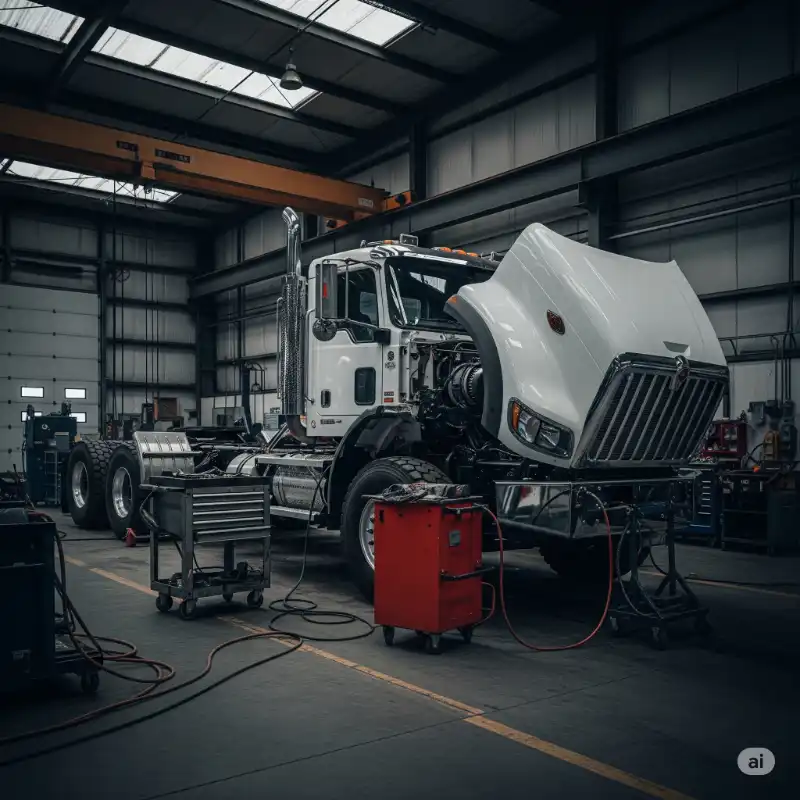
Why Investing in Quality Parts Saves Money on Heavy-Duty Repairs
Why Investing in Quality Parts Saves Money on Heavy-Duty Repairs
Discover why using quality parts for heavy-duty trucks reduces repair costs, improves performance, and prevents costly downtime—especially under Texas road conditions.
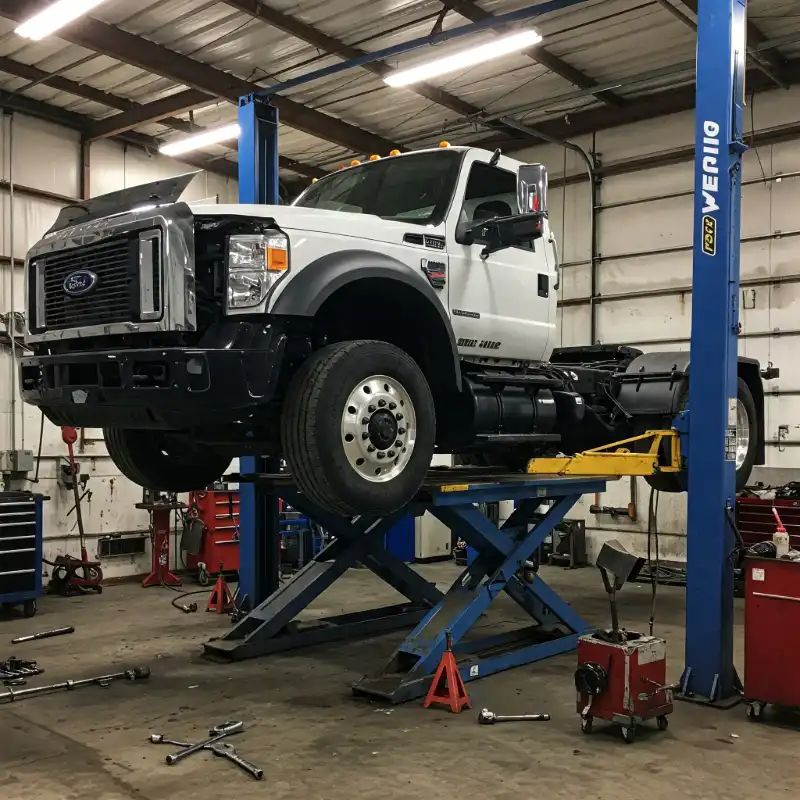
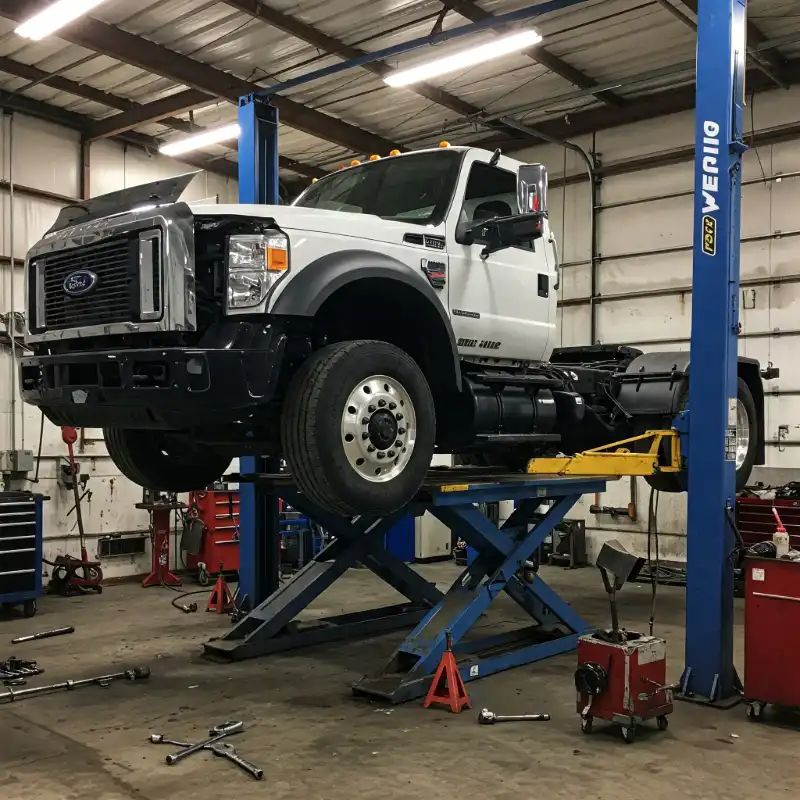
Why Is Summer Maintenance Crucial for Grocery Delivery Fleets?
Why Is Summer Maintenance Crucial for Grocery Delivery Fleets?
Don’t let the Texas heat take down your fleet. Discover how summer maintenance protects grocery delivery trucks, keeps cargo fresh, and ensures reliability all season long.