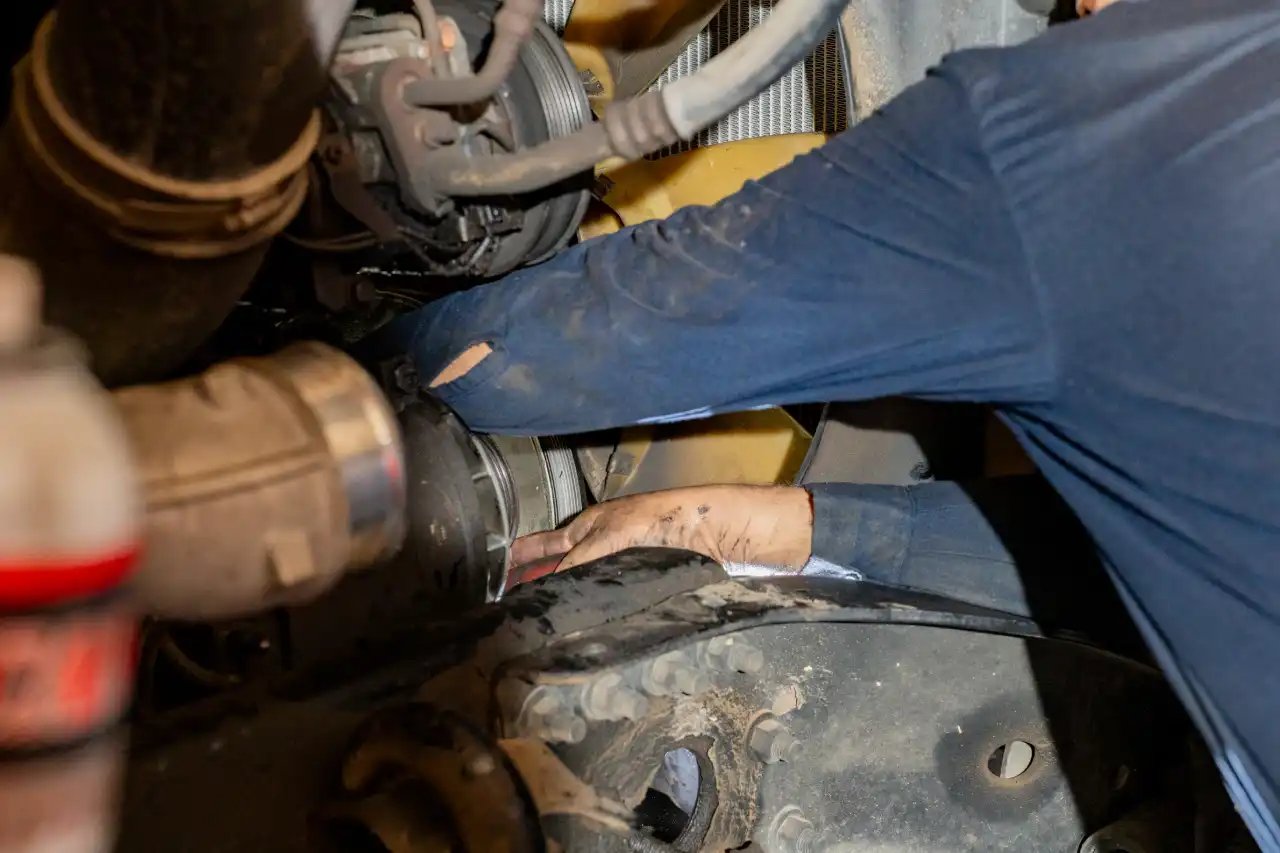
In the bustling world of food and grocery delivery, precision, timing, and care are essential to keeping perishable goods safe from warehouse to shelf. But none of that matters if the driver behind the wheel isn’t trained to handle the rigors of the road, cargo, or compliance.
Whether you're managing a couple of Class 6 box trucks or a full-on Class 8 reefer fleet, how you train your drivers determines your uptime, your compliance rating, and ultimately, your bottom line. And you’re in the right place to learn how to get it right.
Understand the Demands of Perishable Freight
Transporting refrigerated goods isn't your average delivery job. Drivers must be familiar with:
- Temperature control systems and how to adjust reefer settings
- The importance of timely deliveries to prevent spoilage
- Proper loading techniques to maintain airflow and avoid cross-contamination
Before drivers hit the road, they should be fluent in how these systems work and what to do when they don't.
Start With Core Driver Training
Your training program should begin with a foundation in commercial vehicle operations, tailored specifically to food fleets. Cover the following:
Pre-trip inspections: Highlight checks on reefer units, fluid levels, and temperature sensors.
Defensive driving techniques: Especially critical in urban delivery zones where congestion is constant.
DOT regulations: Make sure they’re crystal clear on HOS rules, especially if your routes cross state lines.
And don’t just rely on lectures—use ride-alongs, simulator training, and even mock DOT inspections to drill in practical knowledge.
Include Sanitation and Safety Protocols
Food-grade hauls come with added responsibility. Your drivers must understand:
- The importance of a clean cargo area
- How to properly secure and separate loads
- When and how to report temperature breaches or contamination risks
Teaching this early on helps prevent costly claims and ensures your fleet complies with FSMA (Food Safety Modernization Act) regulations.
Emphasize the Use of In-Cab Technology
Your trucks likely aren’t running blind. From ELDs to reefer monitoring systems, drivers should be trained to:
- Read and respond to alerts from in-cab systems
- Use GPS routing that avoids low bridges or weight-restricted roads
- Submit digital delivery confirmations and log HOS accurately
The more comfortable they are with the tech, the smoother your fleet runs.
Prepare for Texas Roads and Weather
Operating in Texas comes with its own set of rules. Between blistering summers, sprawling highways, and unexpected ice storms, your drivers need to:
- Understand how heat affects reefer performance
- Adjust tire pressure and coolant levels in extreme conditions
- Know alternate routes during seasonal road closures or hurricane disruptions
Training that accounts for regional quirks means fewer surprises and safer trips.
Reinforce Continuous Learning
Driver training shouldn't end after onboarding. Create an environment of ongoing education by:
- Offering refresher courses every quarter
- Conducting post-incident reviews to identify training gaps
- Inviting experienced drivers to mentor new recruits
This builds a culture of safety and excellence from within.
Foster Soft Skills for Customer-Facing Situations
Let’s face it: your drivers are often the face of your business. Train them to:
- Communicate professionally with store managers or receiving clerks
- Handle delivery disputes with tact
- Maintain a neat appearance and follow uniform policies
A good attitude at the loading dock can make the difference between a one-time drop and a long-term account.
Prioritize Physical and Mental Wellness
Let’s not forget: grocery delivery involves early mornings, long hours, and physical strain. Drivers need training on:
- Safe lifting and loading techniques
- Managing fatigue and stress
- Finding healthy food options on the road
A healthy driver is a safer, more efficient one.
Final Thoughts
Building a high-performing food and grocery fleet starts with rock-solid driver training. From equipment know-how to customer service etiquette, the more prepared your drivers are, the smoother your operations—and your margins—will be.
At Integrity Fleet, we’ve got years of experience looking after grocery fleets. If you need a helping hand getting yours ready for the road, we’re always here to help. To get in touch, just tap:
More Articles
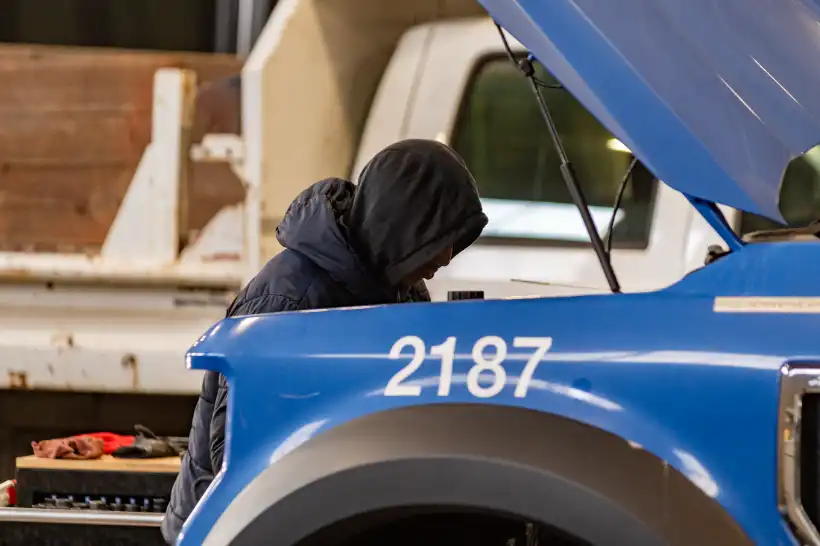
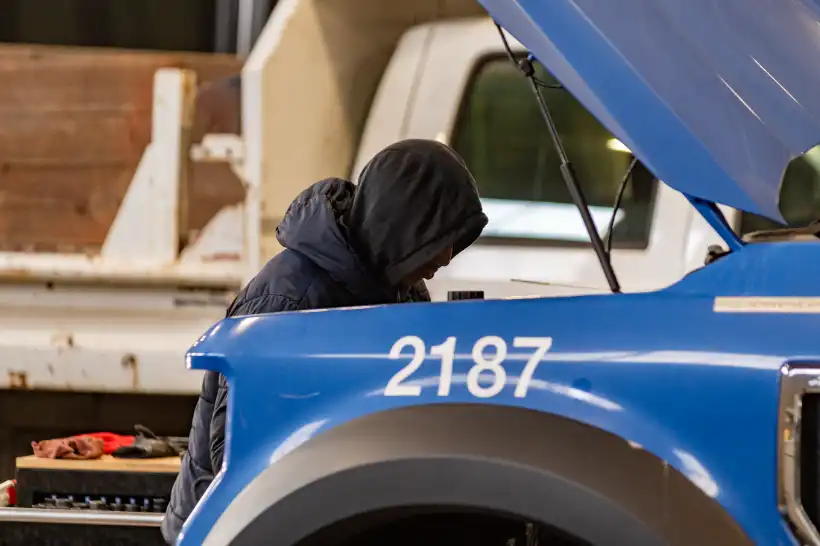
Why Efficient Fleet Management Is Critical for Food and Grocery Deliveries
Why Efficient Fleet Management Is Critical for Food and Grocery Deliveries
Food delivery fleets face no margin for error. In Texas, heat and distance push systems to their limits. From cold chain logistics to cost-saving fuel tactics, this guide explores how efficient fleet management keeps perishables fresh, drivers happy, and profits intact.
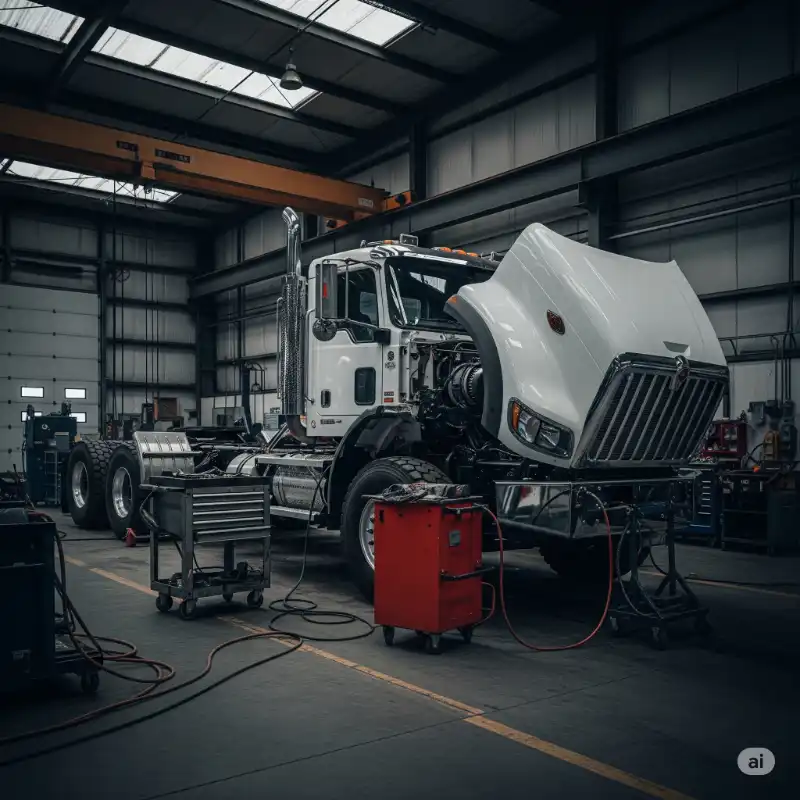
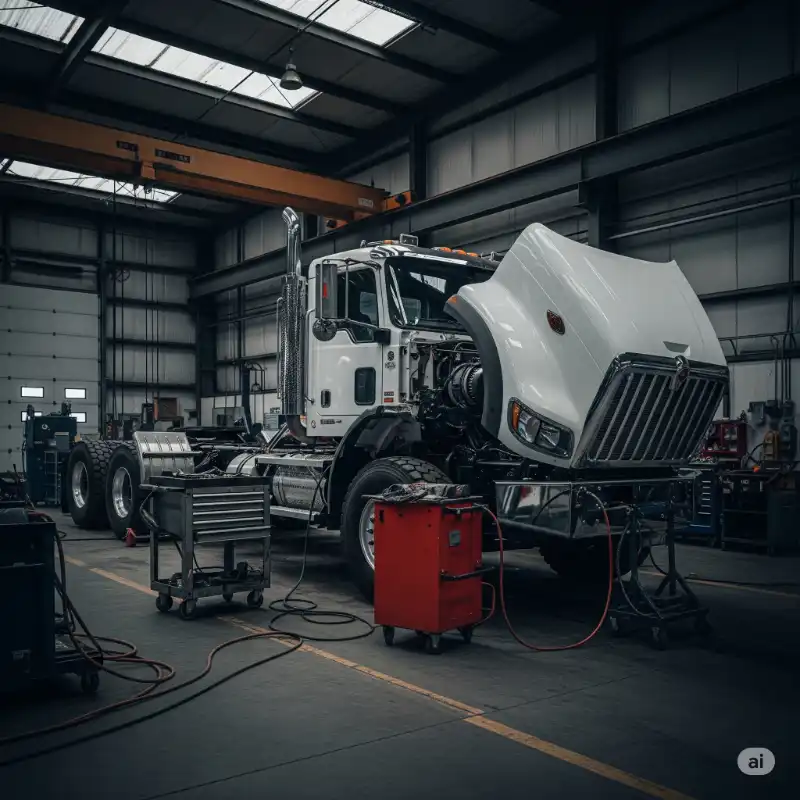
Why Investing in Quality Parts Saves Money on Heavy-Duty Repairs
Why Investing in Quality Parts Saves Money on Heavy-Duty Repairs
Discover why using quality parts for heavy-duty trucks reduces repair costs, improves performance, and prevents costly downtime—especially under Texas road conditions.
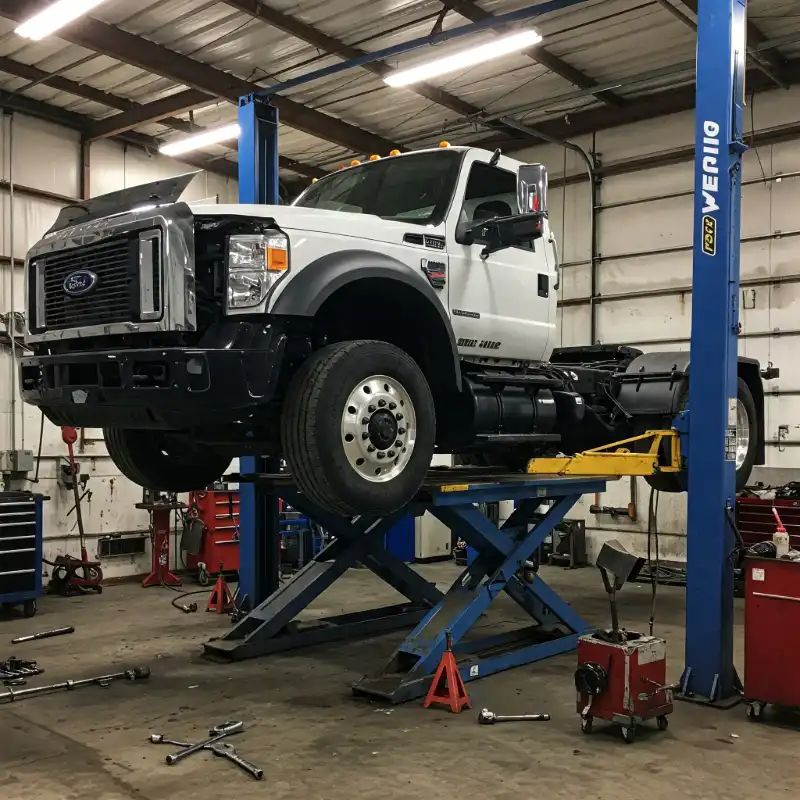
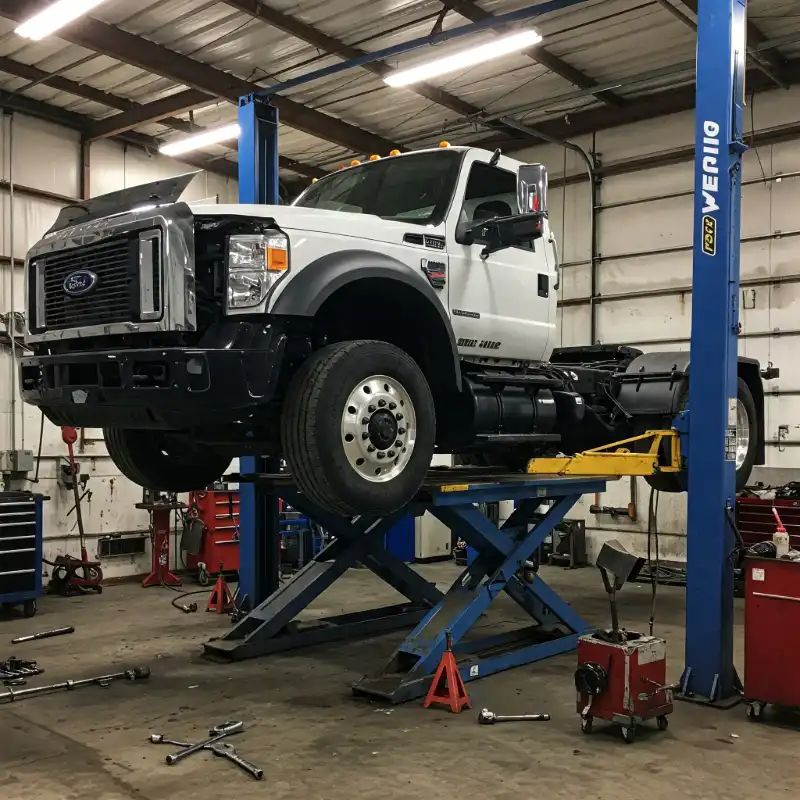
Why Is Summer Maintenance Crucial for Grocery Delivery Fleets?
Why Is Summer Maintenance Crucial for Grocery Delivery Fleets?
Don’t let the Texas heat take down your fleet. Discover how summer maintenance protects grocery delivery trucks, keeps cargo fresh, and ensures reliability all season long.